Induction Heating Vessels / Batch Reactors
Welcome to Interpower Induction, one of the fastest growing induction heating companies in the world
Induction Heating Vessels / Batch Reactors
We have over 30 years experience in induction heating and have developed, designed, manufactured, installed and commissioned Vessel and Pipe Heating systems to many countries all over the world.
Properties
Due to the heating system being naturally simple and very reliable, the option of heating by induction should be regarded as the preferred choice.
Induction heating embodies all the conveniences of electricity taken direct to the process and transformed to heat exactly where it is required. It can be applied successfully to virtually any vessel or pipe system needing a source of heat.
Induction offers many benefits unobtainable by other means and gives improved plant production efficiency and better operating conditions since there is no significant emission of heat to the surroundings. The system is particularly suitable for close control reaction processes such as the production of synthetic resins in a Hazard Area.
As each induction heating vessel is bespoke to each customers specific needs and requirements, we offer varying sizes with differing heat up rates. Our engineers have had many years of experience in evolving custom built induction heating systems for a wide range of applications in a wide range of industries. Heaters are designed to suit the precise requirements of the process and are constructed for quick fitting onto the vessel either in our works or on site.
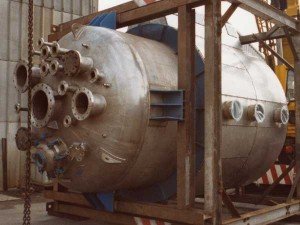
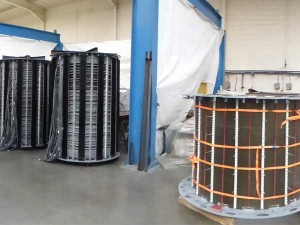
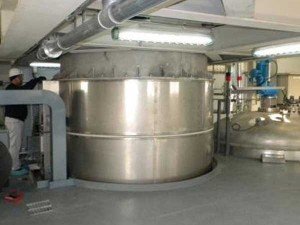
• No physical contact between induction coil and heated vessel wall.
• Rapid start-up and shut-down. No thermal inertia.
• Low heat loss
• Precision product and vessel wall temperature control without over shoot.
• High energy input. Ideal for automatic or micro-processor control
• Safe hazard area or standard industrial operation at line voltage.
• Pollution free uniform heating at high efficiency.
• Low running costs.
• Low or high temperature working.
• Simple and flexible to operate.
• Minimum maintenance.
• Consistent product quality.
• Heater self-contained on vessel generating minimum floor space requirement.
Induction heating coil designs are available to suit metallic vessels and tanks of most forms and shapes in current use. Ranging from a few centremetres to several metres diameter or length. Mild steel, clad mild steel, solid stainless steel or non ferrous vessels can all be successfully heated. Generally a minimum wall thickness of 6mm is recommended.
Unit rating designs range from 1KW to 1500KW. With induction heating systems there is no limit on power density input. Any limitation that exists is imposed by the maximum heat absorption capacity of the product, process or metallurgical characteristics of the vessel wall material.
Induction heating embodies all the conveniences of electricity taken direct to the process and transformed to heat exactly where it is required. Since heating takes place direct in the vessel wall in contact with the product and the heat losses are extremely low, the system is highly efficient (up to 90%).
Induction heating offers a great many benefits unobtainable by other means and gives improved plant production efficiency and better operating conditions since there is no significant emission of heat to the surroundings.
• Reactors and kettles
• Adhesive and special coatings
• Chemical, gas and oil
• Food processing
• Metallurgical and metal finishing
• Air and Gas heating for Chemical and Food Processing
• Hot Oil Heating for Process and Edible Oils
• Vaporising and Superheating: Instant steam raising, low and high temperature / pressure (up to 800ºC at 100 bar)
Reactors and Kettles, Autoclaves, Process Vessels, Storage and Settling Tanks, Baths, Vats and Still Pots, Pressure Vessels, Vapourisors and superheaters, Heat Exchangers, Rotary Drums, Pipes, Dual Fuel Heated Vessels
High Pressure Super Heated Steam heaters, Regenerative Air Heaters, Lubricating Oil Heaters, Edible Oil and Cooking Oil Heaters, Gas heaters including Nitrogen, Nitrogen Argon and Catalytic Rich Gas (CRG) heaters.